xH4 polymeroxid®HARTELOXAL 
Polymeroxid® xH4 is a hard anodizing process optimized not only for glide but also for hardness.
General information
After two years of development and many series of tests in the technical laboratory, we are now ready to present to you the xH4® process. This is a further development of the well-established and widely used H-type process, which is the best hard anodised coating on the market. The technology focuses on achieving maximum wear resistance with the lowest possible coating roughness. This has been achieved through the development of an entirely new advanced monomer-enriched acidic electrolyte and the refinement of other important process parameters.
Features
In order to protect the highly sensitive aluminium material from wear and tear, we offer our XH4® type polymeroxide layer. By developing a completely new polymer matrix, we were able to optimise virtually all application-specific properties. The oxide structure is modified by cross-linked polymers. This leads to exceptional wear protection, increased bending fatigue strength, improved friction levels, reduced slip effects also in cold welding protection.
polymeroxid® - xH4® outperforms even the best coatings of our competitors in terms of the quality of its special properties by up to 30%.
polymeroxid® - xH4 creates the smoothest oxide surface on the market.
Details
Properties of the coating
Fully cross-linked polymer coating throughout the thickness section.
The completely new polymeroxid®-matrix:
- maximum abrasion resistance
- smoother, less rough coating than its competitors
- high hardness of approx. 500 HV 0, 25 (7075-T6)
- very good glide properties
- reduction of the slip-stick effect
- protection against cold welding
- very high flexural strength
Materials
Recommended alloys , we generally cover most of the aluminium alloys used, although the copper content in the alloy should not exceed 5%.
Most commonly used: AlZnMgCu1.5 (7075) , AlMg4.5Mn (5083), AlMgSi0.5/1.0 (6060/6082).
Hardness of the coating
The effective hardness of the coating depends very much on the aluminium alloy used.
For xH4, the process achieves a hardness in the region of 500 - 520 MHV 0.025 (7076 T6).
Areas of application
Automation, Precision Engineering, Hydraulics, Food Industry, Aerospace, Engineering, Medical, Off-shore applications, Petrochemicals, Pharmaceuticals, Pneumatics, Racing, Robotics, Packaging Machinery, Printing Industry, Military Industry, Mining Industry, Textile Industry.
Dimensional accuracy
Polymeroxid® - xH4 coating builds up outside the base material approximately 40% of the total coating thickness (see photo).
Example: 50µm of hard anode means a growth of approx. 20µm (approx. 40µm on diameter). The optimum thickness of this coating is in the range of 30 - 50 microns.
Production capacity
Window size : 4200 x 1450 x 350 mm (automatic line Murowana Goślina)
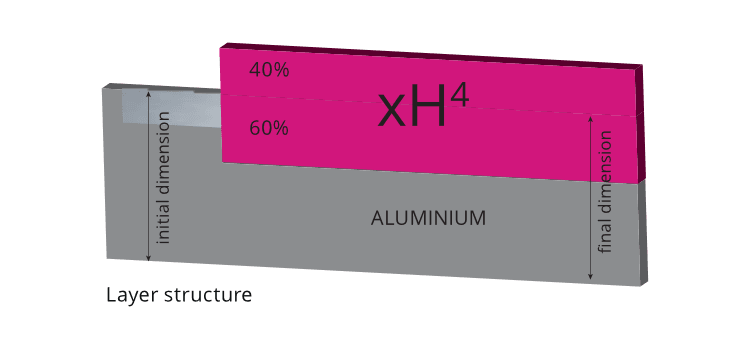